αSTEP AR Series
AR98MA-N5-2
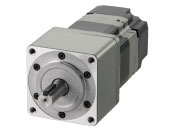
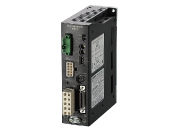
Motor/Control Circuit
Product Classification | Product Name | List Price | List Price | Shipping Date |
---|---|---|---|---|
Geared Motor / Control Circuit | AR98MA-N5-2 | SGD 2,063 | USD 1,650 | Discontinued Product (31.3.2020 discontinued) |
Included
- Motor, Control Circuit, Parallel Key, Motor Connection Cable (2 m), Cable for Electromagnetic Brake (2 m), I/O Signal Connector, Connector for Regeneration Resistor Input/Main Power Input Terminals, 24 VDC Power Supply Input/Regeneration Resistor Thermal Input/Electromagnetic Brake Output Terminal, Connection lever, Operation manual
Specifications
Dimensions
Data Download
Other Specifications
Driver Specifications
Built-in Controller Type | Pulse input type | |||
---|---|---|---|---|
Input/Output Function | Maximum Input Pulse Frequency | − | Line driver output by host controller: 500 kHz (at 50 % duty) Open-Collector Output by Host Controller: 250 kHz (at 50 % duty)*1 Negative Logic Pulse Input (Initial value) |
|
Number of Positioning Data Sets | 64 Points | − | ||
Direct Input | 8 Points | 8 Points | ||
Direct Output | 6 Points | 9 Points | ||
RS-485 Communication Network Input | 16 Points | − | ||
RS-485 Communication Network Output | 16 Points | − | ||
Setting Tool | Data Setting Software MEXE02 | ◯ | ◯ | |
Control Module OPX-2A | ◯ | ◯ | ||
Operation | Positioning Operation | Single-motion Operation | ◯ | − |
Linked Operation | ◯ | − | ||
Sequential Operation | ◯ | − | ||
Direct Operation | ◯ | − | ||
Push-Motion Operation | ◯ | ◯*2 | ||
Continuous Operation | ◯ | − | ||
Return-to-Home Operation | ◯ | − | ||
JOG Operation/Test Operation | ◯ | ◯*2 | ||
Monitor/Warning | Waveform Monitoring | ◯ | ◯ | |
Overload Detection | ◯ | ◯ | ||
Overheat Detection (Motor and Driver) | ◯ | ◯ | ||
Position/Speed Information | ◯ | ◯ | ||
Temperature Detection (Motor and Driver) | − | − | ||
Motor Load Factor | − | − | ||
Travel Distance , Cumulative Travel Distance | − | − | ||
Alarm | ◯ | ◯ |
- *1
- The value when the general-purpose cable (CC36D1E) (sold separately) is used.
- *2
- Setting with extended function (MEXE02 or OPX-2A)
Note
- Do not perform push-motion operation using geared types. Doing so may damage the motor or gearhead.
General Specifications
Motor | Driver | |||
---|---|---|---|---|
Built-in Controller Type | Pulse input type | |||
Thermal Class | 130 (B) | − | ||
Insulation Resistance |
100 MΩ or more when a 500 VDC megger is applied between the following places:
|
100 MΩ or more when a 500 VDC megger is applied between the following places:
|
||
Dielectric Strength |
Sufficient to withstand the following for 1 minute:
|
Sufficient to withstand the following for 1 minute: | ||
|
|
|||
Operating Environment (In operation) | Ambient Temperature | -10 ~ +50 °C (Non-freezing)*1: Standard type,TH,PS, PN, PF
Geared Types 0 ~ +40 ˚C (non-freezing)*1: Harmonic geared type |
0 ~ +55 °C (Non-freezing)*2 | 0 ~ +50 °C (Non-freezing)*2 |
Ambient Humidity | 85 % max. (Non-condensing) | |||
Atmosphere | No corrosive gases or dust. No exposure to water, oil or other liquids. | |||
Degree of Protection | Standard Type (Single shaft), Geared Type: IP65 (excluding mounting surface and connector part) Standard Type (Double shaft), PF Geared Type: IP20 |
IP10 | IP20 | |
Stop Position Accuracy |
AR46: ±4 arc minute (±0.067˚) AR66, AR69, AR98, AR911: ±3 arc minute (±0.05˚) |
|||
Shaft Runout | 0.05 T.I.R. (mm) *3 | − | ||
Concentricity of Installation Pilot to the Shaft |
0.075 T.I.R. (mm) *3 | − | ||
Perpendicularity of mounting surface to the shaft | 0.075 T.I.R. (mm) *3 | − |
- *1
- When a heat sink of a capacity at least equivalent to an aluminum plate with a size of 250×250 mm and 6 mm thickness
- *2
- When a heat sink of a capacity at least equivalent to an aluminum plate with a size of 200×200 mm and 2 mm thickness
- *3
- T.I.R. (Total Indicator Reading): The total dial gauge reading when the measurement section is rotated 1 revolution centered on the reference axis center.
Note
- Disconnect the motor and driver when measuring insulation resistance, or conducting a dielectric strength test.
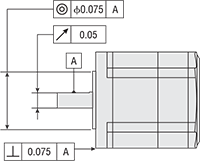
Electromagnetic Brake Specifications
Product Name | AR24 | AR26 | AR46 | AR66 | AR69 | AR98 |
---|---|---|---|---|---|---|
Type | Power off activated type | |||||
Power Supply Voltage | 24 VDC ±5 %*1 | |||||
Power Supply Current [A] | 0.05 | 0.08 | 0.25 | |||
Brake Activation Time*2 [ms] | 20*3 | |||||
Brake Release Time*2 [ms] | 50*3 | 30*3 | ||||
Time Rating | Continuous |
- *1
- For products with an electromagnetic brake, a 24 VDC ±4 % specification applies if the wiring distance is extended to 20~30 m using a cable.
- *2
- This specification is for use with a DC input pulse input type driver.
- *3
- This is the value when the included varistor is used. [Recommended Varistor: Z15D121 (SEMITEC Corporation)]
Rotation Direction
This indicates the rotation direction when viewed from the output shaft side.
The rotation direction of the gearhead output shaft relative to the standard type motor output shaft varies depending on the gear type and gear ratio. Please check the following table.
Type | Gear Ratio | Rotation Direction as Viewed From the Motor Output Shaft Side |
---|---|---|
TS Geared Type | 3.6, 7.2, 10 | Same direction |
20, 30 | Opposite direction | |
TH Geared Type Frame size 28 mm |
7.2, 10 | Opposite direction |
20, 30 | Same direction | |
TH Geared Type Frame size 42 mm, 60 mm, 90 mm |
3.6, 7.2, 10 | Same direction |
20, 30 | Opposite direction | |
SH Geared Type Frame size 28 mm |
7.2, 36 | Same direction |
9, 10, 18 | Opposite direction | |
SH Geared Type Frame size 42 mm, 60 mm |
3.6, 7.2, 9, 10 | Same direction |
18, 36 | Opposite direction | |
SH Geared Type Frame size 90 mm |
3.6, 7.2, 9, 10, 18 | Same direction |
36 | Opposite direction | |
CS Geared Type | 5, 10, 15, 20 | Same direction |
FC Geared Type PS Geared Type PN Geared Type HPG Geared Type |
Overall gear ratio | Same direction |
Harmonic Geared Type | 50, 100 | Opposite direction |
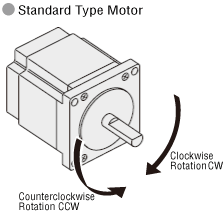
Permissible Moment Load (Harmonic Geared Type)
Motor Frame Size | Permissible Axial Load (N) | Permissible Moment Load (N·m) | Constant a (m) |
---|---|---|---|
20 mm | 60 | 0.7 | 0.00485 |
30 mm | 140 | 2.9 | 0.0073 |
42 mm | 220 | 5.6 | 0.009 |
60 mm | 450 | 11.6 | 0.0114 |
The moment load can be calculated with the following formula.
-
Example 1: When an external force F (N) is applied to a position that extends L (m) horizontally from the center of the output flange
-
Example 2: When external force F (N) is applied to a position that extends in the vertical direction L (m) from the output flange-mounting surface.
Permissible Radial Load and Permissible Axial Load
Type | Motor Frame Size |
Product Name | Gear Ratio | Permissible Radial Load | Permissible Axial Load | ||||
---|---|---|---|---|---|---|---|---|---|
Distance From Shaft End [mm] | |||||||||
0 | 5 | 10 | 15 | 20 | |||||
Standard Type | 20 mm | ARM14, ARM15 | − | 12 | 15 | - | - | - | 3 |
28 mm | ARM24, ARM26 | 25 | 34 | 52 | - | - | 5 | ||
42 mm | ARLM46, ARM46 | 35 | 44 | 58 | 85 | - | 15 | ||
60 mm | ARLM66, ARM66, ARLM69, ARM69 |
90 | 100 | 130 | 180 | 270 | 30 | ||
85 mm | ARLM98, ARM98, ARLM911, ARM911 |
260 | 290 | 340 | 390 | 480 | 60 | ||
TH Geared Type | 28 mm | ARM24 | 7.2, 10, 20, 30 | 15 | 17 | 20 | 23 | − | 10 |
42 mm | ARLM46, ARM46 | 3.6, 7.2, 10, 20, 30 |
10 | 14 | 20 | 30 | − | 15 | |
60 mm | ARLM66, ARM66 | 70 | 80 | 100 | 120 | 150 | 40 | ||
90 mm | ARLM98, ARM98 | 220 | 250 | 300 | 350 | 400 | 100 | ||
PS Geared Type | 28 mm | ARM24 | 5, 7.2, 10 | 45 | 60 | 80 | 100 | − | 40 |
42 mm | ARLM46, ARM46 | 5 | 70 | 80 | 95 | 120 | - | 100 | |
7.2 | 80 | 90 | 110 | 140 | - | ||||
10 | 85 | 100 | 120 | 150 | - | ||||
25 | 120 | 140 | 170 | 210 | - | ||||
36 | 130 | 160 | 190 | 240 | - | ||||
50 | 150 | 170 | 210 | 260 | - | ||||
60 mm | ARLM66, ARM66 | 5 | 170 | 200 | 230 | 270 | 320 | 200 | |
7.2 | 200 | 220 | 260 | 310 | 370 | ||||
10 | 220 | 250 | 290 | 350 | 410 | ||||
25 | 300 | 340 | 400 | 470 | 560 | ||||
36 | 340 | 380 | 450 | 530 | 630 | ||||
50 | 380 | 430 | 500 | 600 | 700 | ||||
90 mm | ARLM98, ARM98 | 5 | 380 | 420 | 470 | 540 | 630 | 600 | |
7.2 | 430 | 470 | 530 | 610 | 710 | ||||
10 | 480 | 530 | 590 | 680 | 790 | ||||
25 | 650 | 720 | 810 | 920 | 1070 | ||||
36 | 730 | 810 | 910 | 1040 | 1210 | ||||
50 | 820 | 910 | 1020 | 1160 | 1350 | ||||
PN Geared Type | 28 mm | ARM24 | 5, 7.2, 10 | 45 | 60 | 80 | 100 | − | 40 |
42 mm | ARLM46, ARM46 | 5 | 80 | 95 | 120 | 160 | − | 100 | |
7.2 | 90 | 110 | 130 | 180 | − | ||||
10 | 100 | 120 | 150 | 200 | − | ||||
60 mm | ARLM66, ARM66 | 5 | 240 | 260 | 280 | 300 | 330 | 200 | |
7.2 | 270 | 290 | 310 | 340 | 370 | ||||
10 | 300 | 320 | 350 | 380 | 410 | ||||
25 | 410 | 440 | 470 | 520 | 560 | ||||
36 | 360 | 410 | 480 | 570 | 640 | ||||
50 | 360 | 410 | 480 | 570 | 700 | ||||
90 mm | ARLM98, ARM98 | 5 | 370 | 390 | 410 | 430 | 460 | 600 | |
7.2 | 410 | 440 | 460 | 490 | 520 | ||||
10 | 460 | 490 | 520 | 550 | 580 | ||||
25 | 630 | 660 | 700 | 740 | 790 | ||||
36 | 710 | 750 | 790 | 840 | 900 | ||||
50 | 790 | 840 | 890 | 940 | 1000 | ||||
Harmonic Geared Type | 30 mm | ARM24 | 50, 100 | 100 | 135 | 175 | 250 | − | 140 |
42 mm | ARLM46, ARM46 | 180 | 220 | 270 | 360 | 510 | 220 | ||
60 mm | ARLM66, ARM66 | 320 | 370 | 440 | 550 | 720 | 450 | ||
90 mm | ARLM98, ARM98 | 1090 | 1150 | 1230 | 1310 | 1410 | 1300 | ||
FC Geared Type | 42 mm | ARM46 | 7.2, 10, 20, 30 | 180 | 200 | 220 | 250 | − | 100 |
60 mm | ARM66 | 270 | 290 | 310 | 330 | 350 | 200 |
- The product names are listed such that the product names are distinguishable.
- PS, PN Geared Type: the value satisfies a calculated lifetime of 20,000 hours when either the permissible radial load or the permissible axial load are applied.
Click here for information about gearhead lifetime
Note
- The output shaft on the back shaft side of the motor output shaft of the double shaft product is for slit plate installation. Do not apply load torque, radial load, and axial load.
Radial Load and Axial Load
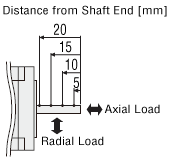
Standards
Regulations and Standards Materials
Documents about compliance with regulations and standards can be downloaded from the "Data Download" tab on the product details page.
(The types of files available for download vary by product.)
Explanations of the Global Laws, Regulations and Standards can be found here.
Information about our compliance with regulations and standards for each of our product series can be found here.
Hazardous Substances
The product does not contain any substances (10 substances) exceeding the regulation values of the RoHS Directive (2011/65/EU, 2015/863/EU).
System Configuration
Cables and Accessories
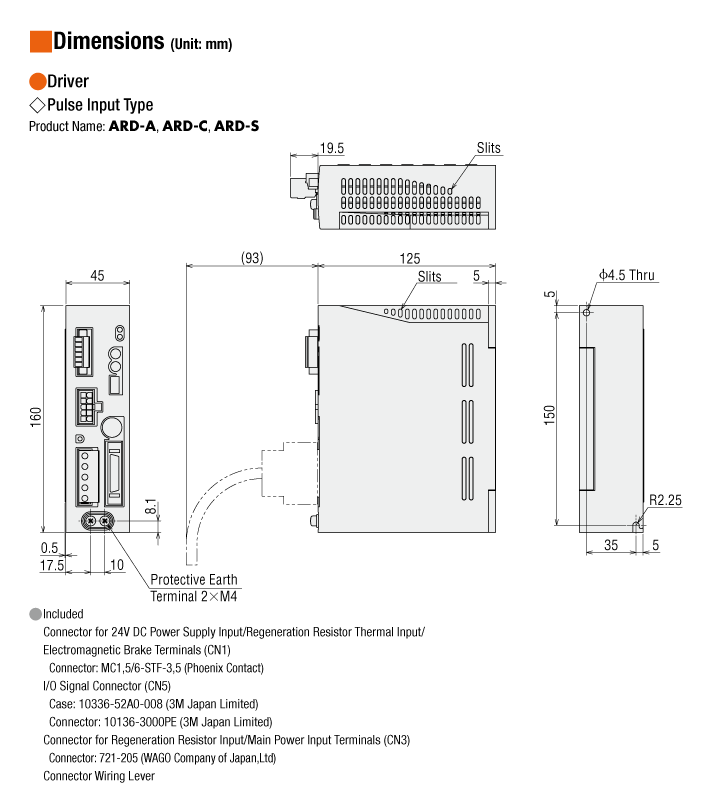