Stepper Motors CMK Series
CMK243BP-SG3.6
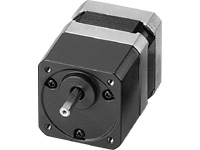
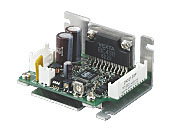
Motor/Control Circuit
Product Classification | Product Name | List Price | List Price | Shipping Date |
---|---|---|---|---|
Motor / Control Circuit | CMK243BP-SG3.6 | SGD 409 | USD 327 | Discontinued Product (31.3.2020 discontinued) |
Included
- Motor, Control Circuit, Connector Housing, Contact, Mounting Screw, Operating Manual
Specifications
Data Download
Other Specifications
Circuit Specifications
Input Signals | Input Mode | Photocoupler Input CW Pulse (pulse) Signal, CCW Pulse (Rotation direction) Signal: Input resistance 200 Ω, Input current 5~20 mA Photocoupler "ON": +3 ~ 5.25V Photocoupler "OFF": 0 ~ +1V (voltage between terminals) Output current off signal, step angle switching signal, and automatic current cutback release signal: Input resistance 3.3 kΩ Input current 1 mA (at 5 VDC)/8 mA (at 24 VDC) Photocoupler "ON": +4.5~26.4 V, Photocoupler "OFF": 0~+1 V (voltage between terminals) |
---|---|---|
CW Pulse Signal (Pulse signal) |
CW direction operation command pulse signal (operation command pulse signal when in 1-pulse input mode), negative logic pulse input Pulse width 5 μs min., rise/fall time 2 μs max., pulse duty 50 % max. When the pulse input is turned from "ON" to "OFF," the motor rotates 1 step. Maximum input pulse frequency 100 kHz (at 50 % pulse duty) |
|
CCW Pulse Signal (Rotation direction signal) |
CCW direction movement command pulse signal (for 1-pulse input mode, rotation direction signal Photocoupler ON: CW, Photocoupler OFF: CCW) photocoupler "OFF": CCW) Negative logic pulse input Pulse width 5 μs min., rise/fall time 2 μs max., pulse duty 50 % max. When the pulse input is turned from "ON" to "OFF," the motor rotates 1 step. Maximum input pulse frequency 100 kHz (at 50 % pulse duty) |
|
All Windings Off Signal | When the photocoupler is "ON," the output current to the motor is turned "OFF," and the motor shaft can be turned by external force. When the photocoupler is "OFF," output current to the motor is turned "ON." |
|
Step Angle Select Input Signal | When the photocoupler is "ON," the motor operates at the basic step angle regardless of how the step angle setting switches are set. When the photocoupler is "OFF," operates at the step angle set by the step angle setting switch. |
|
Automatic current cutback release signal |
When the photocoupler is "ON," the automatic current cutback function is canceled at motor standstill. When the photocoupler is "OFF," the automatic current cutback function will be activated at motor standstill (after approx. 100 ms). |
|
Output Signals | Output Mode | Photocoupler and Open-Collector Output External Use Condition: 24 VDC max., 10 mA max. |
Excitation Timing Signal |
This signal is output when the excitation sequence is step "0." (Photocoupler "ON") [For High-Torque Type and Standard Type] Example)
1.8°/step (number of divisions - 1): Output once every 4 pulses
0.45°/step (number of divisions - 4): Output once every 16 pulses [For High-Resolution Type] Example)
0.9°/step (number of divisions - 1): Output once every 4 pulses
0.225°/step (number of divisions - 4): Output once every 16 pulses [For SH Geared Type (Gear ratio: 18)] Example)
0.1°/step (number of divisions - 1): Output once every 4 pulses
0.025°/step (number of divisions - 4): Output once every 16 pulses |
|
Function | Automatic current cutback, step angle switching, pulse input mode switching, all windings off, excitation timing | |
Cooling Method | Natural cooling method |
General Specifications
Specifications | Motor | Driver | |
---|---|---|---|
Thermal Class | 130 (B) | − | |
Insulation Resistance | 100 MΩ or more when a 500 VDC megger is applied between the motor windings and the case under normal ambient temperature and humidity. | − | |
Dielectric Strength | Under normal ambient temperature and humidity, no abnormalities were observed even if 1.0 kV at 50 Hz or 60 Hz is applied between the windings and the case of the motor for 1 minute. (0.5 kV for frame sizes of 42 mm max.) |
− | |
Operating Environment (In operation) | Ambient Temperature | -10~+50 °C (Non-freezing) | 0~+40 °C (Non-freezing) |
Ambient Humidity | 85 % max. (Non-condensing) | ||
Atmosphere | No corrosive gases or dust. No exposure to water, oil or other liquids. | ||
Temperature Rise | 2-phase excitation at rated voltage, winding temperature rise of 80 °C max. at standstill (Resistance change method) | − | |
Stop position accuracy*1 | ±3 arc minute (±0.05˚) | − | |
Shaft Runout | 0.05 T.I.R. (mm)*4 | − | |
Radial Play*2 | 0.025 mm Max. (Load 5 N) | − | |
Axial Play*3 | 0.075 mm Max. (Load 10 N) [CMK22□ Load 2.5 N] |
− | |
Concentricity of Installation Pilot to the Shaft | 0.075 T.I.R. (mm)*4 | − | |
Perpendicularity of mounting surface to the shaft | 0.075 T.I.R. (mm)*4 | − |
- *1
- This is the value at full step and no load (Varies depending on the size of the load).
- *2
- Radial Play: Displacement in shaft position in the radial direction when a 5 N load is applied perpendicular to the tip of the motor shaft.
- *3
- Axial Play: Displacement in shaft position in the axial direction when a 10 N load (CMK22□ is 2.5 N) is applied to the motor shaft in the axial direction.
- *4
- T.I.R. (Total Indicator Reading): The total dial gauge reading when the measurement section is rotated 1 revolution centered on the reference axis center.
Note
- Do not measure insulation resistance or perform a dielectric strength test while the motor and driver are connected.
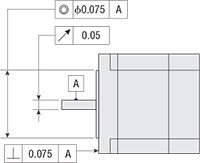
Permissible Radial Load and Permissible Axial Load
Type | Motor Frame Size | Motor Product Name | Gear Ratio | Permissible Radial Load | Permissible Axial Load | ||||
---|---|---|---|---|---|---|---|---|---|
Distance From Shaft End [mm] | |||||||||
0 | 5 | 10 | 15 | 20 | |||||
High-Torque Type | 20 mm | PK213P, PK214P, PK513P | - | 12 | 15 | - | - | - | 3 |
28 mm | PK223P, PK224P, PK225P, PK523P, PK525P, PK523HP, PK525HP |
25 | 34 | 52 | - | - | 5 | ||
35 mm | PK233P, PK235P | 20 | 25 | 34 | 52 | - | 10 | ||
42 mm | PK244P, PK246P, PK544P, PK546P | 20 | 25 | 34 | 52 | - | 10 | ||
56.4 mm | PK264P, PK266P, PK268P | 61 | 73 | 90 | 110 | 160 | 20 | ||
High-Torque and High-Efficiency Type | 42 mm | PKE243, PKE244, PKE245 | 20 | 25 | 34 | 52 | - | 10 | |
High-Resolution Type / High-Resolution Type With Encoder |
28 mm | PK523PM, PK524PM, PK525PM, PK523HPM, PK524HPM, PK525HPM |
25 | 34 | 52 | - | - | 5 | |
42 mm | PK243M, PK244M, PK245M, PK544PM, PK546PM |
20 | 25 | 34 | 52 | - | 10 | ||
56.4 mm | PK264M, PK266M, PK268M | 54 | 67 | 89 | 130 | - | 20 | ||
60 mm | PK564PM, PK566PM, PK569PM | 90 | 100 | 130 | 180 | 270 | 20 | ||
Standard Type / Standard Type Terminal Box Type / Standard Type With Encoder / Standard Type With electromagnetic brake |
42 mm | PK243, PK244, PK245, PK543 PK544, PK545 |
20 | 25 | 34 | 52 | - | 10 | |
50 mm | PK256, PK258 | 54 | 67 | 89 | 130 | - | 20 | ||
56.4 mm | PK264, PK266, PK268 | 54 | 67 | 89 | 130 | - | 20 | ||
60 mm | PK564, PK566, PK569 | 63 | 75 | 95 | 130 | 190 | 20 | ||
85 mm | PK596, PK599, PK5913, PK296 PK299, PK2913 |
260 | 290 | 340 | 390 | 480 | 60 | ||
SH Geared Type | 28 mm | PK223P | 7.2, 9, 10, 18, 36 | 15 | 17 | 20 | 23 | - | 10 |
42 mm | PK243 | 3.6, 7.2, 9, 10, 18, 36, 50, 100 | 10 | 15 | 20 | 30 | - | 15 | |
60 mm | PK264 | 3.6, 7.2, 9, 10 | 30 | 40 | 50 | 60 | 70 | 30 | |
18, 36, 50, 100 | 80 | 100 | 120 | 140 | 160 | ||||
TH Geared Type | 28 mm | PK523P | 7.2, 10, 20, 30 | 15 | 17 | 20 | 23 | - | 10 |
42 mm | PK543 | 3.6, 7.2, 10, 20, 30 | 10 | 14 | 20 | 30 | - | 15 | |
60 mm | PK564 | 70 | 80 | 100 | 120 | 150 | 40 | ||
90 mm | PK596 | 220 | 250 | 300 | 350 | 400 | 100 | ||
PS Geared Type | 22 mm | PK513P | 4, 16 | 20 | 30 | - | - | - | 20 |
28 mm | PK523P | 5, 7.2, 10 | 45 | 60 | 80 | 100 | - | 40 | |
42 mm | PK545 | 5 | 70 | 80 | 95 | 120 | - | 100 | |
7.2 | 80 | 90 | 110 | 140 | - | ||||
10 | 85 | 100 | 120 | 150 | - | ||||
PK543 | 25 | 120 | 140 | 170 | 210 | - | |||
36 | 130 | 160 | 190 | 240 | - | ||||
50 | 150 | 170 | 210 | 260 | - | ||||
60 mm | PK566 | 5 | 170 | 200 | 230 | 270 | 320 | 200 | |
7.2 | 200 | 220 | 260 | 310 | 370 | ||||
10 | 220 | 250 | 290 | 350 | 410 | ||||
PK564 | 25 | 300 | 340 | 400 | 470 | 560 | |||
36 | 340 | 380 | 450 | 530 | 630 | ||||
50 | 380 | 430 | 500 | 600 | 700 | ||||
90 mm | PK599 | 5 | 380 | 420 | 470 | 540 | 630 | 600 | |
7.2 | 430 | 470 | 530 | 610 | 710 | ||||
10 | 480 | 530 | 590 | 680 | 790 | ||||
PK596 | 25 | 650 | 720 | 810 | 920 | 1070 | |||
36 | 730 | 810 | 910 | 1040 | 1210 | ||||
50 | 820 | 910 | 1020 | 1160 | 1350 | ||||
PN Geared Type | 28 mm | PK523P | 5, 7.2, 10 | 45 | 60 | 80 | 100 | − | 40 |
42 mm | PK544 | 5 | 80 | 95 | 120 | 160 | − | 100 | |
7.2 | 90 | 110 | 130 | 180 | − | ||||
10 | 100 | 120 | 150 | 200 | − | ||||
60 mm | PK566 | 5 | 240 | 260 | 280 | 300 | 330 | 200 | |
7.2 | 270 | 290 | 310 | 340 | 370 | ||||
10 | 300 | 320 | 350 | 380 | 410 | ||||
PK564 | 25 | 410 | 440 | 470 | 520 | 560 | |||
36 | 360 | 410 | 480 | 570 | 640 | ||||
50 | 360 | 410 | 480 | 570 | 700 | ||||
90 mm | PK599 | 5 | 370 | 390 | 410 | 430 | 460 | 600 | |
7.2 | 410 | 440 | 460 | 490 | 520 | ||||
10 | 460 | 490 | 520 | 550 | 580 | ||||
PK596 | 25 | 630 | 660 | 700 | 740 | 790 | |||
36 | 710 | 750 | 790 | 840 | 900 | ||||
50 | 790 | 840 | 890 | 940 | 1000 | ||||
Harmonic Geared Type | 20 mm | PK513P | 50, 100 | 50 | 75 | - | - | - | 60 |
30 mm | PK523HP | 110 | 135 | 175 | 250 | - | 140 | ||
42 mm | PK543 | 180 | 220 | 270 | 360 | 510 | 220 | ||
60 mm | PK564 | 320 | 370 | 440 | 550 | 720 | 450 | ||
90 mm | PK596 | 1090 | 1150 | 1230 | 1310 | 1410 | 1300 |
- The product names are listed such that the product names are distinguishable.
- PS, PN Geared Type: Standard Input Rotation Speed: 1500 r/m, the value satisfies a calculated lifetime of 20,000 hours when either the permissible radial load or the permissible axial load are applied.
Radial Load and Axial Load
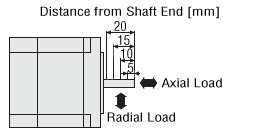
Standards
Regulations and Standards Materials
Documents about compliance with regulations and standards can be downloaded from the "Data Download" tab on the product details page.
(The types of files available for download vary by product.)
Explanations of the Global Laws, Regulations and Standards can be found here.
Information about our compliance with regulations and standards for each of our product series can be found here.
Hazardous Substances
The product does not contain any substances (10 substances) exceeding the regulation values of the RoHS Directive (2011/65/EU, 2015/863/EU).
System Configuration
Cables and Accessories
close