Electric Linear Slides EAS Series (Former type)
EAS4X-E070-K-2
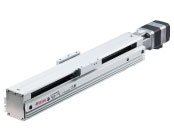
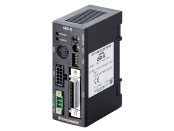
Actuator/Control Circuit
Product Classification | Product Name | List Price | List Price | Shipping Date |
---|---|---|---|---|
Actuator / Control Circuit | EAS4X-E070-K-2 | - | - | Discontinued Product (1.4.2016 discontinued) |
Included
- Actuator, Control Circuit, Motor Cable (2 m), Control I/O Connector, Connector for Main Power Input/Frame Ground Terminals, Operating Manual
Specifications
Other Specifications
Circuit Specifications
Positioning Function Built-in Type |
Pulse Input Type | ||
---|---|---|---|
Maximum Input Pulse Frequency | − | Line Driver output by Host Controller: 500 kHz (at 50 % duty) Open-Collector Output by Host Controller: 250 kHz (at 50 % duty)* |
|
Number of Positioning Data Sets | 64 Points | − | |
Positioning Operation | Independent | ◯ | − |
Linked | ◯ | − | |
Linked 2 | ◯ | − | |
Sequential | ◯ | − | |
Direct | ◯ | − | |
Continuous Operation | ◯ | − | |
JOG Operation | ◯ | − | |
Return-To-Home Operation | ◯ | − | |
Test Operation | ◯ | ◯ | |
Absolute-position backup system | ◯ | − | |
Control Module OPX-2A | ◯ | ◯ | |
Support Software MEXE02 | ◯ | ◯ |
- *The value is when using a general-purpose cable (sold separately).
RS-485 Communication Specifications
Protocol | Modbus Protocol (Modbus RTU mode) |
---|---|
Electrical Characteristics | EIA-485 Compliant Use twisted-pair cables (TIA/EIA-568B CAT5e or better recommended). The max. total extension length is 50 m. |
Transmission/Reception Mode | Half duplex |
Transmission Rate | 9600bps/19200bps/38400bps/57600bps/115200bps |
Physical Layer | Asynchronous mode (Data: 8 bits, Stop Bit: 1 bit or 2 bits, Parity: none, even, or odd) |
Connection Type | Maximum 31 units can be connected to a single programmable controller (master device). |
General Specifications
DC Input
Motor | Driver | |||
---|---|---|---|---|
Positioning Function Built-in Type |
Pulse input Input type |
|||
Thermal Class | 130(B) | − | ||
Insulation Resistance |
100 MΩ or more when 500 VDC megger is applied between the following places.
|
100 MΩ or more when 500 VDC megger is applied between the following places.
|
- | |
Dielectric Strength |
Sufficient to withstand the following for 1 minute.
|
Sufficient to withstand the following for 1 minute.
|
- | |
Operating Environment (When operating) |
Ambient Temperature | 0~+50 °C (Non-freezing) When sensor set (accessory) is installed 0~+40 °C (Non-freezing) |
0~+50 °C (Non-freezing) | |
Ambient Humidity | 85 % max. (Non-condensing) | |||
Atmosphere | No corrosive gases or dust. No exposure to water, oil or other liquids. | |||
Degree of Protection | IP40 (IP20 for motor part connector) | IP10 | IP20 |
Note
- Do not perform the insulation resistance test or the dielectric strength test while the actuator and driver are connected.
AC Input
Motor | Driver | |||
---|---|---|---|---|
Positioning Function Built-in Type |
Pulse input Input type |
|||
Thermal Class | 130(B) | − | ||
Insulation Resistance |
100 MΩ or more when 500 VDC megger is applied between the following places.
|
100 MΩ or more when 500 VDC megger is applied between the following places.
|
||
Dielectric Strength |
Sufficient to withstand the following for 1 minute.
|
Sufficient to withstand the following for 1 minute: | ||
|
|
|||
Operating Environment (When operating) |
Ambient Temperature | 0~+50 °C (Non-freezing) When sensor set (accessory) is installed 0~+40 °C (Non-freezing) |
0~+55 °C (Non-freezing)* | 0~+50 °C (Non-freezing)* |
Ambient Humidity | 85 % max. (Non-condensing) | |||
Atmosphere | No corrosive gases or dust. No exposure to water, oil or other liquids. | |||
Degree of Protection | IP40 (IP20 for motor part connector) | IP10 | IP20 |
- *When installing a heat sink equivalent to an aluminum plate min. 200×200 mm, thickness 2 mm
Note
- Do not perform the insulation resistance test or the dielectric strength test while the actuator and driver are connected.
Travel Direction
At the time of shipment, the travel direction of the table is set as follows.
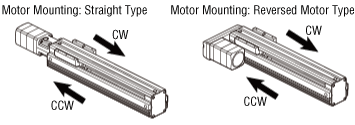
Calculating Load Moment
When a load is transported with an electric linear slide or electric cylinder (a unit equipped with shaft guide covers only), the load moment acts on the linear guide/shaft guide if the position of the load's center of gravity is offset from the center of the table/center of the shaft guide. The direction of action applies to the directions for pitching (MP), yawing (MY), and rolling (MR), depending on the position of the offset.
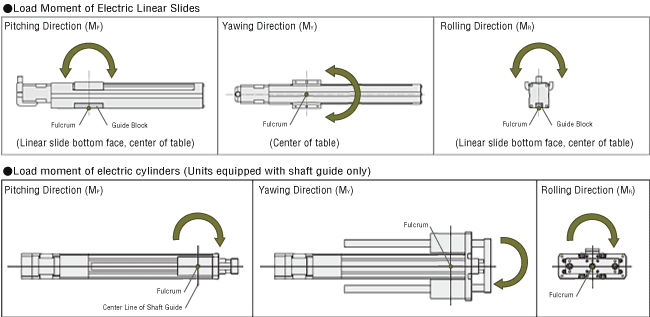
Even though the selected electric actuators satisfy the load mass and positioning time requirements, when the center of gravity of the load is overhung from the table's center/shaft guide’s center, the run life may decrease as a result of the load moment. Load moment calculations must be completed and whether the conditions are within specifications values must be checked. The moment applied under static conditions is the static permissible moment. The moment applied under movement is the dynamic permissible moment, and both must be checked.
Calculate the load moment of the electric linear slides and electric cylinders (units equipped with shaft guide covers only) based on loads that are applied. Check that the static permissible moment and dynamic permissible moment are within limits and check that strength is sufficient.
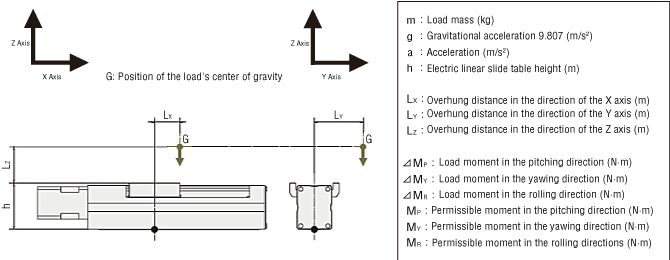
- *For more information on calculating static permissible moment and dynamic permissible moments, click here.
Load Moment Formula
When there are several overhung loads, etc., it is determined by the sum of moments from all loads.