Hollow Rotary Actuators DGII Series
DG200R-AZMCD-2
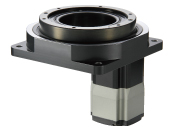
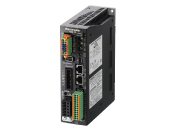
Actuator/Control Circuit
Product Classification | Product Name | List Price | List Price | Shipping Date |
---|---|---|---|---|
Actuator / Control Circuit | DG200R-AZMCD-2 | SGD 4,260 | USD 3,408 | Discontinued Product (31.3.2020 discontinued) |
Included
- Actuator, Circuit, Cable for motor (2 m), Encoder Connection Cable (2 m), Cable for Electromagnetic Brake (2 m), Main Power Supply/Regeneration Resistor Connector (CN4), I/O Signal Connector (CN5), Connector for 24 VDC Power Supply input · Electromagnetic Brake Connector · Regeneration Unit Thermal Input · power removal signal input (CN1), Connection lever, Operation manual
Specifications
Dimensions
Other Specifications
General Specifications (Actuator)
Installed Motor | AZ Series | |
---|---|---|
Operating Environment (When operating) |
Ambient Temperature | 0∼+40°C (Non-freezing)∗ |
Ambient Humidity | 85% max. (Non-condensing) | |
Atmosphere | No corrosive gases or dust. No exposure to water, oil or other liquids. | |
Multi-Rotation Detection Range in Power OFF State (Motor output shaft) |
±900 revolutions (1800 revolutions) |
- ∗
- According to Oriental Motor’s measurement conditions
Driver Circuit Specifications
Built-in Controller Type | Pulse input type with RS-485 communication | Pulse input type | ||||
---|---|---|---|---|---|---|
I/O function | Maximum Input Pulse Frequency | - | Line driver output from host controller: 1 MHz (at 50 % duty) Open-Collector Output by Host Controller: 250 kHz (at 50 % duty) Negative logic pulse input |
|||
Number of Positioning Data Sets | 256 points | 256 points* | ||||
Direct Input | 10 points | 6 points | ||||
Direct Output | 6 points | |||||
RS-485 communication remote input | 16 points | - | ||||
RS-485 communication remote output | 16 points | - | ||||
Setting Tool | Support Software MEXE02 | ○ | ||||
Coordinates Management Method | Battery-free Absolute System | |||||
Operation | Positioning Operation |
Product Line | Positioning Operation | ○ | ○ | ○※ |
Fastening method | Single-motion Operation | ○ | ○ | ○※ | ||
Sequential Operation | ○ | ○ | ○※ | |||
Multistep Speed-Change (Configuration Connection) | ○ | ○ | ○※ | |||
Sequence Control |
Loop Operation (Repeating) | ○ | ○ | ○※ | ||
Event Jump Operation | ○ | ○ | ○※ | |||
Continuous Operation | Position Control | ○ | ○ | ○※ | ||
Speed Control | ○ | ○ | ○※ | |||
Torque control | ○ | ○ | ○※ | |||
Return-To-Home Operation | Return-To-Home Operation | ○ | ○ | ○ | ||
High-speed return-to-home operation | ○ | ○ | ○ | |||
JOG Operation | ○ | ○ | ○ | |||
Monitor/Information | Waveform Monitoring | ○ | ○ | ○ | ||
Overload Detection | ○ | ○ | ○ | |||
Overheat Detection (Motor and Driver) |
○ | ○ | ○ | |||
Position/Speed Information | ○ | ○ | ○ | |||
Temperature Detection (Motor and Driver) |
○ | ○ | ○ | |||
Motor Load Factor | ○ | ○ | ○ | |||
Travel Distance , Cumulative Travel Distance | ○ | ○ | ○ | |||
Alarm | ○ | ○ | ○ |
- *It can be used by setting it with MEXE02 support software.
Circuit General Specifications
|
Built-in Controller Type Pulse Input Type with RS-485 Communication EtherNet/IP Compatible EtherCAT Compatible PROFINET Compatible |
Pulse Input Type MECHATROLINK-III Compatible SSCNET III/H Compatible |
|
---|---|---|---|
Insulation Resistance |
100 MΩ or more when a 500 VDC megger is applied between the following places:
|
||
Dielectric Strength |
Sufficient to withstand the following for 1 minute:
|
||
Operating Environment (When operating) |
Ambient Temperature | 0~+55 °C (Non-freezing)* | |
Ambient Humidity | 85 % max. (Non-condensing) | ||
Atmosphere | No corrosive gases or dust. No exposure to water, oil or other liquids. | ||
Degree of Protection | IP10 | IP20 | |
Multi-Rotation Detection Range in Power OFF State (Motor output shaft) |
± 900 revolutions (1800 revolutions) |
- *When installing a heat sink equivalent to an aluminum plate min. 200×200 mm, thickness 2 mm
Note
- Disconnect the motor and driver when conducting insulation resistance measurements or the dielectric strength test.
Also, do not conduct these tests on the ABZO sensor part of the motor.
RS-485 Communication Specifications
Protocol | Modbus RTU Mode |
---|---|
Electrical Characteristics | EIA-485 Compliant, Straight Cable Use twisted-pair cables (TIA/EIA-568B CAT5e or better recommended). The max. total extension length is 50 m.* |
Mode | Half duplex communication and asynchronous mode (data: 8 bits, stop bit: 1 bit or 2 bits, parity: none, even, or odd) |
Transmission Rate | 9600 bps, 19200 bps, 38400 bps, 57600 bps, 115200 bps, and 230400 bps are available. |
Connection Type | Up to 31 units can be connected to a single programmable controller (master device). |
- *If a specific wiring and layout causes the motor cable or power supply cable to generate a noise problem, shield the cable or use ferrite cores.
System Configuration
Related Products
Products | Features | ||
---|---|---|---|
NETC02-CC![]() |
Features |
[CC-Link Ver. 2 Compatible] By supporting CC-Link Ver.2, you can simplify the ladder program and shorten the communication time for data sending and receiving. |
|
Products |
NETC01-CC![]() |
Features |
[CC-Link Ver.1.1 Compatible] By connecting a network converter, you can complete the wiring process with a single dedicated cable approved for the CC-Link communication protocol. |
Products |
NETC01-M2![]() |
Features |
[MECHATROLINK-II Compatible] By connecting a network converter, the wiring process can be completed with a single dedicated cable approved for the MECHATROLINK-II communication protocol. |
Products |
NETC01-M3![]() |
Features |
[MECHATROLINK-III Compatible] By connecting a network converter, the wiring process can be completed with a single dedicated cable approved for the MECHATROLINK-III communication protocol. |
Products |
NETC01-ECT![]() |
Features |
[EtherCAT Compatible] |
Cables and Accessories
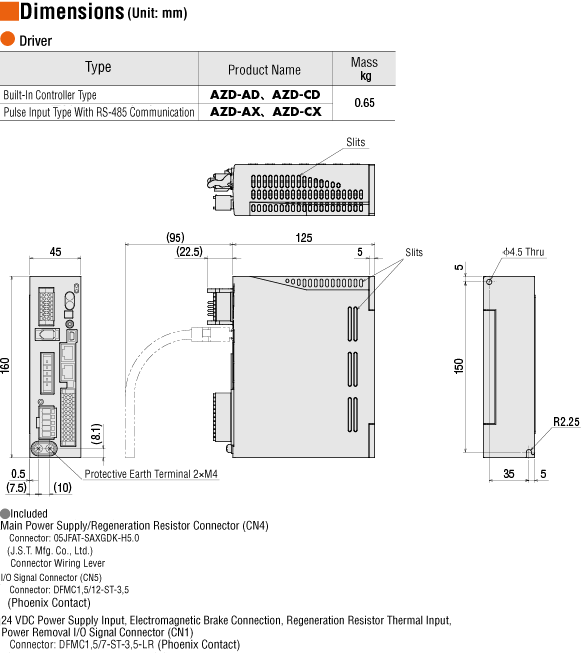