Brushless Motors BX Series
BX6400S-200S+OPX-1A
Product Classification | Product Name | List Price | List Price | Shipping Date |
---|---|---|---|---|
Gearhead / Motor / Control Circuit | BX6400S-200S | SGD 1,785 | USD 1,428 | Discontinued Product (31.3.2019 discontinued) |
Control Module | OPX-1A | SGD 250 | USD 200 | Discontinued Product (31.3.2019 discontinued) |
Components
Motor/Control Circuit/Gearhead | BXM6400-GFS(Motor)/BXD400A-S(Control Circuit)/GFS6G200(Gearhead) |
---|
Included
- Motor and Driver Package: Motor, Gearhead, Control Circuit, External Speed Potentiometer (with Signal Line), Mounting Bracket for Control Circuit (with Screws), Mounting Screws, Parallel Key, Operating Manual
Data Setter: Data Setter, Dedicated Communication Cable (2 m)
Specifications
Data Download
Other Specifications
Common Specifications
Item | Specifications |
---|---|
Input Signals* | Photocoupler input method Input resistance 2.3kΩ Internal power supply voltage +15V CW input, CCW input, speed data selection input, motor control release (FREE) input, Brake input (at alarm output: alarm reset input) |
Output Signals* | Open-collector output 4.5~26.4 VDC Alarm output, busy output (at alarm output: alarm pulse output): 40 mA max. Speed output ASG, BSG: 20mA or less |
Protective Function | When the following protective functions are activated, the motor will coast to a stop, (Electromagnetic brake motors will be braked) and alarm output will be turned off. The driver alarm LED will be blinking the number of times shown in parentheses (alarm pulses will be output).
|
Maximum Extension Distance | Motor and driver distance 20.4 m (when an accessory connection cable is used) |
Time Rating | Continuous |
-
The available input signals and output signals differ between the basic model and the system upgrade and between the speed control mode and the position control mode when the system is upgraded.
General Specifications
Item | Motor | Driver | |
---|---|---|---|
Insulation Resistance | 100 MΩ or more when a 500 VDC megger is applied between the windings and the case after continuous operation under normal ambient temperature and humidity. (Except for the encoder) |
After continuous operation at normal ambient temperature and humidity, the measurement value between the power supply terminal and the case and the power supply terminal and the I/O signal terminal is 100 MΩ min. using a 500 VDC megger. |
|
Dielectric Strength | No abnormality is observed even with an application of 1.5 kVAC at 50 Hz between the coils and the case for 1 minute after continuous operation at normal ambient temperature and humidity. (Except for the encoder) |
No abnormality is observed even with an application of 1.5 kVAC at 50 Hz between the power supply terminal and the case or 1.8 kVAC at 50 Hz between the power supply terminal and the I/O signal terminal for 1 minute after continuous operation at normal ambient temperature and humidity. |
|
Temperature Rise | After rated continuous operation at normal ambient temperature and humidity, the measured value using the thermocouple method is 50 °Cmax. for the temperature rise of the coils and 40 °C max. *1 for the temperature rise on the case surface. |
After rated continuous operation at normal ambient temperature and humidity, the measurement value of the temperature rise of the heat sink is 50 °C max. using the thermocouple method. |
|
Operating Environment | Ambient Temperature | 0∼+50°C (Non-freezing) | |
Ambient Humidity | 85 % max. (Non-condensing) | ||
Altitude | Up to 1000 m above sea level | ||
Atmosphere | Cannot be used in special environments such as corrosive gas, no dust, radioactive materials, magnetic fields, or vacuums | ||
Vibration | Not subject to continuous vibration or excessive shock In conformance with JIS C 60068-2-6, "Sine-wave vibration test method" Frequency Range: 10~55 Hz, Half Amplitude: 0.15 mm, Sweep Direction: 3 directions (X, Y, Z), Number of Sweeps: 20 times |
||
Storage Conditions*2 | Ambient Temperature | -20∼+60°C (Non-freezing) | -25~+70°C (Non-freezing) |
Ambient Humidity | 85 % max. (Non-condensing) | ||
Altitude | Up to 3000 m above sea level | ||
Thermal Class | UL/CSA Standards: 105 (A), EN Standards: 120 (E) | − | |
Degree of Protection | IP54 (Excluding the installation surface of the round shaft type and connectors) | IP10 |
- *1
- Attach round shaft types to a heat sink (Material: aluminum) of one of the following sizes to maintain a motor case surface temperature of 90 °C max.
30 W Type: 115×115 mm, 5 mm thickness, 60 W Type: 135×135 mm, 5 mm thickness, 120 W Type: 165×165 mm, 5 mm thickness,
200 W Type: 200×200 mm, 5 mm thickness, 400 W Type: 250×250 mm, 6 mm thickness - *2
- The value for storage condition applies to short periods such as the period during transport.
Note
- Do not measure insulation resistance or perform a dielectric strength test the motor and driver are connected.
Speed Control Specifications
- Standard Model: These specifications apply when using the basic motor and driver package.
- When the System is Upgraded: These specifications apply when using the control module sold separately (OPX-1A or MEXE01).
Item | Standard Model | When the System is Upgraded |
---|---|---|
Speed Control Range | 30~3000 r/min (at analog Setting) | 30~3000 r/min (at analog Setting) 3~3000 r/min (setting in 1 r/min units at digital setting) |
Speed Setting Methods | Select one of the following methods.
|
Select one of the following methods.
|
Acceleration Time and Deceleration Time | 0.1∼15 sec. (3000 r/min at no load) Acceleration Time and Deceleration Time are common to all Speed Data |
Select one of the following methods. (3000 r/min at no load)
|
Multi-Speed Setting Methods |
2-Speed:
*1-Speed by Internal Speed Potentiometer and 1-Speed by External Speed Potentiometer (20kΩ, 1/4W) or External DC Voltage (0~5VDC)
|
Select one of the following methods.
|
Position Control Specifications
These are the specifications when the control module (OPX-1A or MEXE01) is added and used in the position control mode.
Positioning Operation
Item | Specifications |
---|---|
Position Setting Mode | Incremental (relative position from the present position) Method |
Resolution | 0.72˚ (500 steps/1 revolution) |
Data Setting Number | 6 points (Data No. 0~No. 5) |
Travel Amount Setting Range | -8 388 608~+8 388 607 steps (data No. 0~No. 5) |
Speed Setting Range | 30~3000 r/min (at analog Setting) 3~3000 r/min (setting in 1 r/min units at digital setting) |
Speed Setting Methods | Select one of the following methods.
|
Acceleration Time and Deceleration Time | Select one of the following methods. (3000 r/min at no load)
|
Continuous Operation
Item | Specifications |
---|---|
Data Setting Number | 2 points *1 (1 unit of data No. 0~No. 1 is assigned to continuous operation) |
Speed Setting Range | 30~3000 r/min (at analog Setting) 3~3000 r/min (setting in 1 r/min units at digital setting) |
Speed Setting Methods | Select one of the following methods.
|
Acceleration Time and Deceleration Time | Select one of the following methods. (3000 r/min at no load)
|
Rotation Direction | 0 min.: CW -1 max.: CCW (setting of rotation direction is done by travel amount) |
- *1
- When used in continuous operation, the number of positioning operation data is 4 points, from data No. 2~No. 5.
Return-to-Mechanical Home Operation
Item | Specifications |
---|---|
Mechanical Home Detection Method | 1-Sensor Mode (Normally closed) |
Start Direction of Home Detection | CW or CCW |
Speed Setting Range | 3~3000 r/min (setting in 1 r/min units at digital setting) Data No. 7 |
Return-to-Electrical Home Operation
Item | Specifications |
---|---|
Travel Amount | Moves from motor standstill position to the electrical home |
Electrical Home Offset Amount Setting Range | -8 388 608~+8 388 607 steps |
Initial Value of Electrical Home Offset Amount | 0 |
Speed Setting Range | 3~3000 r/min (setting in 1 r/min units for digital setting) Data No. 6 |
Acceleration Time and Deceleration Time | Select one of the following methods. (3000 r/min at no load)
|
Torque Limiting Function
Adding the control module (OPX-1A or MEXE01) allows setting of limits on the output torque of the motor in speed control mode and position control mode.
Item | Specifications |
---|---|
Torque Limiting Setting Command | Select one of the following methods.
|
Torque Limiting Setting Range | Assuming that the starting torque value of the motor is 100 %, setting of torque limiting values can be in the following ranges.
|
Note
- An error of approximately ±20 % maximum (Starting Torque: 100 %) may occur between the setting value and generated torque due to the setting speed, power supply voltage, or motor cable extension distance.
Accuracy for repetition under the same conditions is about ±10%.
Permissible Radial Load and Permissible Axial Load
Combination type with a parallel shaft gearhead
Product Name | Gear Ratio | Permissible Radial Load | Permissible Axial Load N |
|
---|---|---|---|---|
10 mm From Shaft End N |
20 mm From Shaft End N |
|||
BX230■-□S | 5 | 100 | 150 | 40 |
10, 15, 20 | 150 | 200 | ||
30, 50, 100, 200 | 200 | 300 | ||
BX460■-□S | 5 | 200 | 250 | 100 |
10, 15, 20 | 300 | 350 | ||
30, 50, 100, 200 | 450 | 550 | ||
BX5120■-□S | 5 | 300 | 400 | 150 |
10, 15, 20 | 400 | 500 | ||
30, 50, 100, 200 | 500 | 650 | ||
BX6200■-□S BX6400S-□S BX6400SM-□S |
5, 10, 15, 20 | 550 | 800 | 200 |
30, 50 | 1000 | 1250 | 300 | |
100, 200 | 1400 | 1700 | 400 |
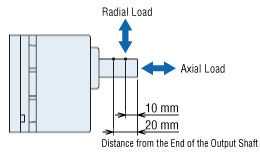
Combination type with a hollow shaft flat gearhead
Product Name | Gear Ratio | Permissible Radial Load | Permissible Axial Load N |
|
---|---|---|---|---|
10 mm From the Gearhead Mounting Surface N |
20 mm From the Gearhead Mounting Surface N |
|||
BX230■-□FR | 5, 10 | 450 | 370 | 200 |
15, 20, 30, 50, 100, 200 | 500 | 400 | ||
BX460■-□FR | 5, 10 | 800 | 660 | 400 |
15, 20, 30, 50, 100, 200 | 1200 | 1000 | ||
BX5120■-□FR | 5, 10 | 900 | 770 | 500 |
15, 20 | 1300 | 1110 | ||
30, 50, 100, 200 | 1500 | 1280 | ||
BX6200■-□FR BX6400S-□FR BX6400SM-□FR |
5*, 10 | 1230 | 1070 | 800 |
15, 20 | 1680 | 1470 | ||
30, 50, 100 | 2040 | 1780 |
- *BX6400S-□FR, BX6400SM-□FR only.
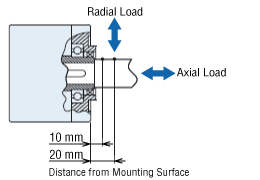
Round Shaft Type
Product Name | Permissible Radial Load | Permissible Axial Load | |
---|---|---|---|
10 mm From Shaft End N |
20 mm From Shaft End N |
||
BX230■-A | 87.2 | 107 | Half of the motor mass or less |
BX460■-A | 117 | 137 | |
BX230■-A | 156 | 176 | |
BX6200■-A BX6400S-A BX6400SM-A |
197 | 221 |
System Configuration
Cables and Accessories
close
close